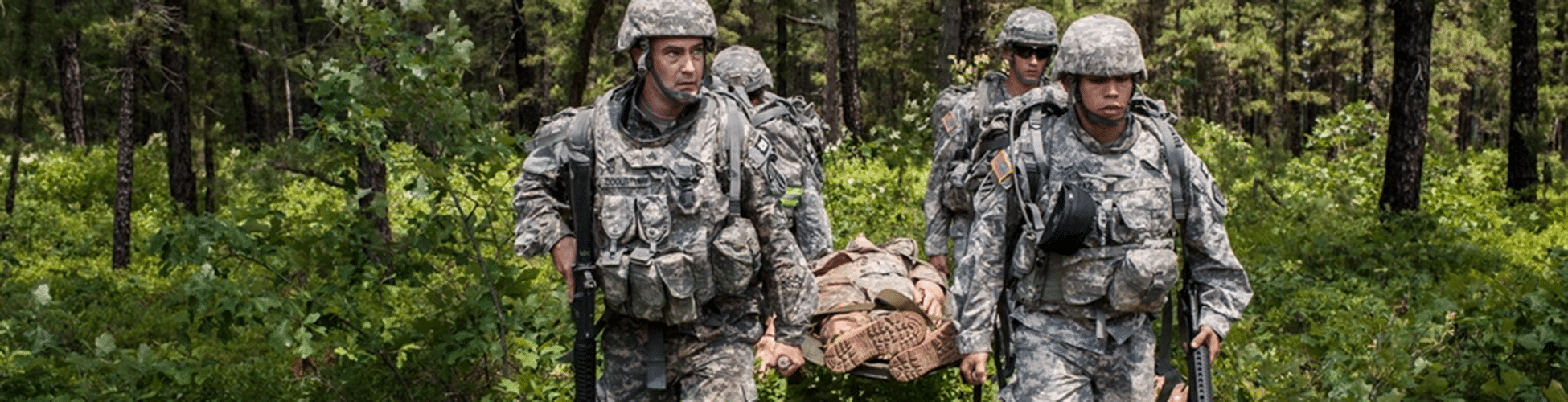
Groundbreaking Exoskeleton Provides Warfighters with Augmented Grip Strength for Litter Transports
Aptima receives DHA contract for ‘GRIPMASTER,’ an innovative exoskeleton solution designed to meet the need for variable assistance in intricate defense operations
Aptima, Inc., a trailblazer in leveraging artificial intelligence and advanced analytics to enhance mission readiness, announced today that it has received a Defense Health Agency (DHA) Phase I Small Business Innovative Research (SBIR) award to develop a quasi-passive hand exoskeleton tailored to enhance grip strength.
GRIPMASTER: Grip Reinforcement Integrated Power with Magnetic Actuation for Seamless Tactical Exoskeleton Response
Modern battlefields necessitate swift evacuation of casualties, predominantly via litter transport, placing immense physical burdens on service members. The challenge is twofold: the weight and awkwardness of carrying the injured, often while providing critical medical care or returning fire, and the rapid exhaustion of grip strength, a pivotal component in this process.
To address this challenge, Aptima, along with partners at the University of Alabama (Huntsville) and SIMETRI, is developing the Grip Reinforcement Integrated Power with Magnetic Actuation for Seamless Tactical Exoskeleton Response (GRIPMASTER) system. This innovative exoskeleton is meticulously tailored to augment grip strength during the demanding task of litter transport. It integrates a cutting-edge sensor suite, capturing intricate hand and wrist movements and couples this with advanced machine learning algorithms. These algorithms not only discern user actions with precision but also proactively anticipate subsequent movements, ensuring fluidity and adaptability. GRIPMASTER’s dynamic locking system permits rapid engagement or disengagement based on situational demands. Furthermore, its predictive capabilities ensure real-time fatigue detection, proactively reducing strain and potential injury risks, making it a groundbreaking solution in military medical evacuations.
By locking and unlocking as per the user’s needs, it will provide much-needed flexibility in tasks. This includes intricate defense operations such as disarming explosives, assembling weaponry, or navigating complex machinery, as well as daily activities such as lifting heavy objects, performing repetitive tasks, or handling precision tools that exert strain on the hand and wrist. Building on the foundation of previously developed machine learning and specialized algorithms from projects designed for lower body manipulation, Aptima’s sophisticated data analytics engine is poised to seamlessly integrate into the GRIPMASTER system. These tried and tested algorithms are pivotal in interpreting sensor data, ensuring the exoskeleton facilitates precise, adaptive responses tailored to the user’s needs.
Aptima’s Sensor-based Assessment Technologies
GRIPMASTER is a member of Aptima’s Sensor-based Assessment Technologies (SAT) portfolio of technologies that utilizes signals from the brain and body to inform performance-optimizing solutions that accelerate learning and optimize human-machine teaming. SAT leverages a wide range of multimodal data, from neuroimaging devices such as EEG and fNIRS, to computerized software for email and cognitive task performance. With SAT, data-derived insights provide objective feedback about individual internal conditions and abilities that would otherwise go unnoticed. As a result, individuals, supervisors, and even computerized co-workers (systems-as-teammates, automated assistants) can make informed adjustments to enhance safety and efficiency.
Aptima welcomes the adoption or merging of your technology with one or more of our SBIR Topics. We are eligible for SBIR Enhancement funding, as well as TACFI and STRATFI awards, all of which are sole source.
For more information, please contact aptima_info@aptima.com.
US Army photo by Timothy L. Hale/Released.